
From AI to the industrial metaverse: The tech cheat sheet for industry
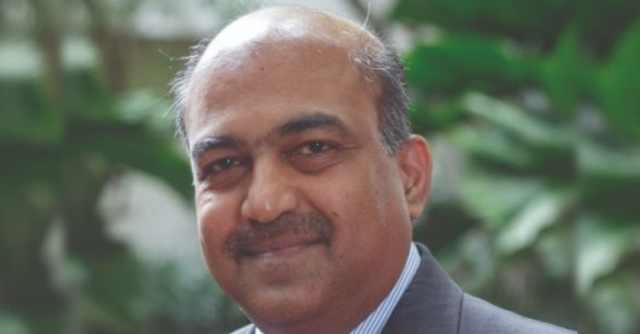

The industrial world is experiencing a data boom like never before. From furnace temperatures and warehouse logistics to smart meters tracking energy use, industries are generating vast amounts of data on countless operational processes. Half of all industrial data has been created in the last two years. Estimates show that another 38% of new operational data will be stored and processed in the cloud in 2024.
In India, technology spending is set to reach around $54.5 billion, with the fastest growth in the Asia Pacific region for 2024. Going forward, how we collate, analyse and collectively leverage this wealth of data will shape future industrial value. And a more connected world can support the responsible use of the world’s resources during an era of unprecedented disruption.
How industrial cloud platforms enhance both internal and external collaboration

Despite the large amounts of industrial data we are collecting, much of these remain siloed and unanalysed. But knowledge is power. It is only when industrial units securely share their data internally and with external partners that they can truly unlock the actionable insights needed to spark innovation and growth.
In India, industrial businesses are increasingly relying on digital twins—virtual models of physical systems—to simulate outcomes and improve decision-making. The local digital twin market is projected to grow nearly 20-fold to $12 billion by 2032, driven by technological advancements and the demand for predictive maintenance.
But cloud data-sharing does not have to be limited to internal stakeholders; it can – and should – be extended to external partners. For example, Pimpri-Chinchwad Municipal Corporation (PCMC) enhanced collaboration across 4,600 individual municipal systems and applications using AVEVA Unified Operations Centre. By working with external parties, PCMC delivered greater impact for its residents and businesses, reducing energy use by more than 15%, cutting water losses by 18%, traffic congestion by more than 20%, and energy use by 18-22%.

Sharing access to the digital twin via the cloud democratises access to information that has the potential to unleash the next wave of industrial transformation.
How AI analytics improve human insight
Just as how data sharing with both internal and external partners via secure channels can deliver massive value, artificial intelligence (AI) too has shown that it can improve our work in very real terms by generating actionable insights that help maximise operational performance.

For example, Japanese petroleum refiner Idemitsu streamlined its scheduling system using cloud and AI technology, enabling the automatic generation of schedules that account for unique operational complexities, supply chain events, and business needs. This saved days of work and left time for higher-value tasks.
Industries are onboarding several AI technologies such as advanced analytics programmes that can effortlessly construct and run no-code AI-driven models, simplifying and optimising production efficiency. For example, by crunching hundreds of variations, AI models enable operators to make confident decisions—while improving profitability and sustainability.
Indian companies are already thinking ‘planet and profit’ instead of ‘planet vs profit’ – with 48% of businesses believing that addressing environmental issues will contribute to business results over the next five years. In the short term, these efficiency gains help reduce energy consumption and greenhouse gas emissions. Over the medium term, AI tools function as an engine of innovation, leading to industrial process improvements and even new value chains.

Likewise, predictive asset and process optimisation can create a hybrid digital twin — blending both physical and simulated data to inform decisions. With such a 360-degree view of asset health and performance, operators can identify problems earlier, establish their causes more accurately, and forecast the time for implementing a solution. Ultimately, feeding these insights back into the design of future assets kicks off a cycle of continuous improvement.
Next, the industrial metaverse will solve real challenges
The metaverse is already making its mark in India with Makers Lab, the research and development branch of Tech Mahindra. The company recently introduced a new project called 'Meta Village.' This digital version of the village Pargaon in Maharashtra aims to make learning fun through the Roblox platform and promote innovation in education.

Similarly, with access to real-time data and intelligent insights democratised across the ecosystem, the stage is set for the next step in industrial transformation: the industrial metaverse.
This game-changing technology is simply a way of bringing teams together virtually to improve efficiency. In the industrial metaverse, people collaborate around a real-time representation of physical assets, with live data and analytics available on command. The adoption of the industrial metaverse will offer businesses a competitive advantage as it enables real-time monitoring and simulation in virtual environments. Some benefits include improved risk management, enhanced training, reduced labour shortages, and more efficient product development.
It is only when industrial entities share their data with internal and external partners that they can truly capitalise on the competitive insights required to drive the next wave of sustainable and revolutionary change.

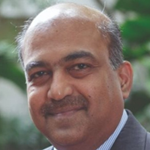
Ajit Kulkarni
Ajit Kulkarni is Vice President and India Market Leader at AVEVA.