
Automation is the answer for staying competitive: Simpolo Ceramics CIO
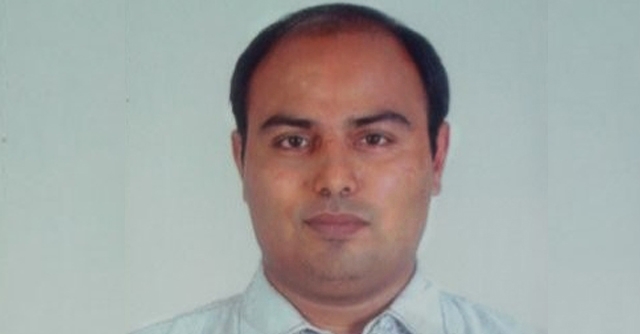

In the past 4-5 years, ceramic tile manufacturing has evolved into a more structured market with new consumers emerging. This growth has been fuelled by the thriving housing and retail sectors, alongside significant technological advancements driving innovation. In an interview with TechCircle, Manish Chandegara, the Chief Information Officer (CIO) at Simpolo Ceramics—a Gujarat-based a premium tiles manufacturer —explores the technological trends shaping this burgeoning industry, the future of technology, and the changing role of CIOs. Edited excerpts.
What technologies excite you for your organisation and the ceramic tiles sector?
While the ceramic tiles sector remains largely fragmented, it has become more organised recently. I am particularly enthusiastic about customer relationship management (CRM), customer experience automation, legacy maintenance, robotic automation, Automated Guided Vehicle (AGV) lifts, and the transition from manual to robotic glazing of tiles. There is an increasing demand for digitally printed tiles, known for their intricate designs that enhance the aesthetics of spaces. Additionally, 3D printing offers manufacturers a vast array of unique designs.
Is your company's tech budget increasing this year? If so, what technologies are you prioritizing?
We are expanding our technology budget as we plan to establish two new facilities across India in the coming 12 months. As recently Motilal Oswal Group has Invested in Simpolo, our investments will focus on advanced technologies such as AI and automation to boost productivity and streamline operations. We will also prioritise business transformation initiatives for rapid adaptation to market changes, along with plant maintenance and cybersecurity, given the convergence of operational technology (OT) and information technology (IT). OT involves hardware and software for monitoring and controlling physical devices, while IT focuses on managing information for business functions. Integrating these domains boosts efficiency, improves data analysis, and enables real-time decision-making by connecting physical and digital systems.
How is the CIO/CTO role changing, and what challenges do they face today?
The role of CIOs and CTOs is becoming increasingly vital in shaping the digital future of organisations. These leaders are now responsible for not only implementing new technologies, but also driving innovation, enhancing operational efficiency, and improving customer experiences—a reality recognised by CEOs and boards. A central challenge for CIOs and CTOs is demonstrating that digital projects deliver measurable returns on investment, a key consideration for board approvals on funding. They must develop clear strategies aligned with organisational objectives and effectively showcase their projects' financial impact through performance metrics and regular evaluations.
What innovations are you introducing through technology? Can you share an example where technology has enhanced business revenues or customer experience?
We achieved a targeted ROI in a previous organisation by migrating our human resource management system (HRMS) to Salesforce, centralising data. Previously, disparate tools and spreadsheets limited our analysis, leading to inefficiencies. By consolidating data in Salesforce, we eliminated silos, reducing manual tasks and unreliable third-party connections. This streamlined our production and delivery processes significantly. However, it is crucial to conduct a thorough risk assessment before starting any migration project.
In terms of competitor benchmarking, what technology areas should you prioritize over the next 12-18 months?
Automation is critical for maintaining a competitive edge, and we focus on quality. High-quality production processes lead to increased production rates and the implementation of advanced automation technologies that streamline operations and reduce errors. As organizations adopt these systems, the demand for skilled technology professionals rises. We are hiring top talent and training our employees in cloud technology, automation, ERP/CRM, and other areas to maintain our competitive advantage.
What is your tech vision for the sector in the next 2-3 years?
Generative AI will increasingly shape the industry, with early adopters already reaping benefits. It enables manufacturers to create complex designs, prototypes, and simulations rapidly, leading to faster time-to-market and cost efficiency. Additionally, generative AI enhances supply chain management, predictive maintenance, and quality control by analysing large data sets to identify trends and potential issues. More organisations will incorporate conversational AI into manufacturing maintenance, allowing for quick issue detection. By integrating voice AI assistants, like Siri, with machinery, we can monitor performance and alert maintenance personnel to potential problems early, thereby reducing downtime and improving efficiency. The AI assistant can also gather data on machine usage and performance, assisting maintenance staff in task prioritisation.
