
Unlocking the Potential: Aligning Industry 4.0 Investments with Quality 4.0
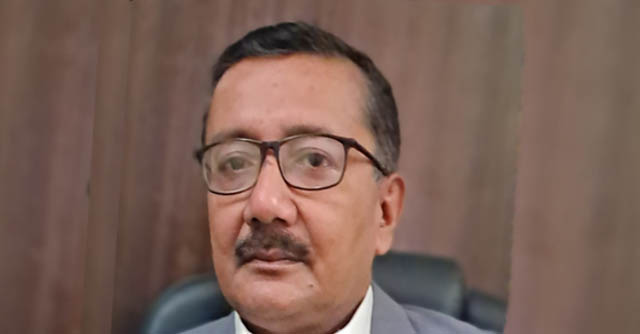

Over the last five years, only a select number of manufacturers globally have successfully integrated Industry 4.0 into their workflow, with some making their way into Industry 5.0 practices. The remaining majority find themselves in the pilot testing phase or trying to work out the best possible way of creating quality ROI.
The challenge is that new technologies can solve many challenges—which leaves manufacturers with the task of deciphering the best solution suited for their needs. This results in either investing in a range of technologies without a sense of direction or investing in limited technologies and trying to solve all challenges. The quality of implementation takes a hit either way.
When done right, Industry 4.0 solutions can increase labor productivity by over 30% and reduce downtime by 40-50%. Hence, it is worth exploring why the Quality 4.0 framework can complement Industry 4.0 solutions and help manufacturers make the most out of their investments.

Quality has no shortcuts
The market has drastically changed since the pandemic. Product life cycles are now shorter, but the demand continues to soar. While this has urged several OEMs to look into high-end automation systems, these systems require meticulous quality checks. Without the right digital innovation support; manufacturers could risk skipping the foundational practices, leading to weaker products with Industry 4.0 technologies.
What this essentially means is that there are levels to tech adoption, each with its own quality check. In the early stages of tech adoption, the focus is primarily on productivity with higher output volumes (quality 1.0). In the second era, quality 2.0, the goal is to maximize labor productivity and reduce scrap and waste. With quality 3.0, manufacturers double down on customer satisfaction and standardisation. And lastly, quality 4.0 involves digitalisation and the adoption of smart technology for the optimal trade-off between quality and productivity.

It is crucial that manufacturers lay down the foundational stones before investing in Quality 4.0. And these processes need not be long and drawn out. Digital engineering solutions providers can support manufacturers through this journey, enabling them to make swift progress.
Potential to scale
Scalability in the Quality 4.0 framework assesses why manufacturers need to invest in industry 4.0 solutions. A big-scale manufacturer would need automated robots that help them load, unload, assemble and pack materials, but ones that are just starting out need not go the extra mile to incorporate that level of automation.

The question isn’t, “Will my business need this in the future?,” it is rather, “Does my business need it right now?”
All kinds of technological investments boil down to the quality of output that it can help the business produce. Does it enhance productivity, production value and improve the bottom line? If so, it meets the standard practices of Quality 4.0, irrespective of the organisation's size.
These decisions can be made easily for a fraction of the cost if businesses make the right strategic collaborations.

Quality beyond tech implementation
According to a BCG study, about two-thirds of manufacturers feel that Quality 4.0 will significantly improve operations within five years. However, just 16% of them have begun implementing Quality 4.0 practices, and 63% haven’t even reached the planning stage. The reason? Businesses forget to look beyond technology.
While technology is an important part of it, Quality 4.0 also relies on people and processes. Ensuring that the workers are experienced in handling the new technologies and that the processes are re-evaluated from the ground up is equally important. Simply put, manufacturers need people to make Industry 4.0 tech work. The better trained and equipped the employees are, the better output manufacturers stand to gain.

It’s the reason why digital innovation vendors often ensure that the businesses they work with are well-equipped to align their Industry 4.0 objectives with their resources at hand.
Quality across the board
Quality 4.0 extends beyond the conventional definitions of quality assurance. It represents a comprehensive approach seamlessly integrating cutting-edge technology, robust processes, and human expertise. By adopting industry 4.0 technologies such as AI, machine learning, and cloud, manufacturers stand to gain a lot more than better ROI. The convergence of Industry 4.0 and Quality 4.0 practices can define innovation, efficiency, and global competitiveness for their business for years to come.

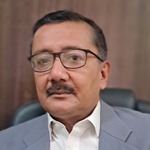
Soumya Bhattacharya
Soumya Bhattacharya, Executive Vice President IoT, AI/ML, Data at Creative Synergies Group