
Researchers use 3D printing for sustainable, smart construction
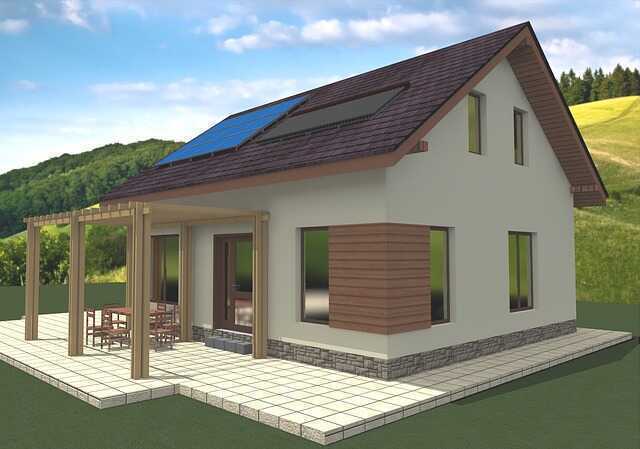

At a time when global experts are looking for a new solution to combat deforestation, researchers from the Massachusetts Institute of Technology (MIT) and the Charles Stark Draper Laboratory have developed a new method of 3D bio-printing wood-like materials to aid sustainable construction.
3D printing or additive manufacturing uses computer-aided designing to make prototypes or working models of objects by laying down successive layers of materials such as thermoplastic, metal, fibre or ceramic, etc. With the help of software, the model to be printed is first developed by the computer, which then gives instructions to the 3D printer.
This technique leverages lab-grown living cells from the Zinnia elegans plant, and can be used to print all manner of custom shapes like chairs, tables, and other wood products without the need to chop down any trees, it said.

“The idea is to grow these plant materials in exactly the shape that you need, so you don’t need to do any subtractive manufacturing after the fact, which reduces the amount of energy and waste. There is a lot of potential to expand this and grow three-dimensional structures,” Ashley Beckwith, lead author of the study, said.
Also read: India’s armed forces turn to 3D printing for military construction work
Trees are a crucial natural resource heralded for their life-sustaining decarbonisation effects, but humans are dwindling its supply via deforestation, said the researcher, adding that the new research can aid in sustainable and smart construction, going forward.

For example, the researchers envision a future where they could bring lab-grown wood products with properties based on their intended applications, like high strength and insulative structures for the walls of buildings.
The 3D printing of wood and wood-like materials is not a new venture. Last year, Massachusetts-based 3D printer OEM Desktop Metal made headlines when it launched its subsidiary Forust, a brand focused on 3D printing functional end-use wood parts via binder jetting.
The global 3D printing market size was valued at $13.84 billion in 2021 and is expected to expand at a compound annual growth rate (CAGR) of 20.8% from 2022 to 2030. Globally, 2.2 million units of 3D printers were shipped in 2021 and the shipments are expected to reach 21.5 million units by 2030.

3D printing is gradually getting mainstream attention in India too, after years of limited adoption, as most industries faced supply chain disruptions during the Covid-19 pandemic. Sectors such as medical, logistics and construction are especially seeing some growth momentum.
Recently, Chennai-based India Cements and deep tech start-up Tvasta Manufacturing Solutions partnered to build more affordable and sustainable housing. “3D-printing in construction employs 30% less water and sand,” the companies said. The duo has worked on projects in Jaisalmer and Gandhinagar for the Indian Air Force (IAF) and an ongoing infrastructure project for a corporate entity in Mumbai.
In February, the Ministry of Electronics and Information Technology (MeitY) under the government of India released a national strategy for 3D printing technology to encourage collaboration between academia, government and industry. It aims at making India a global hub for design, development and deployment of 3D printing.
