
India can make its own battery cells from 2022: Nitin Gupta, CEO, Attero
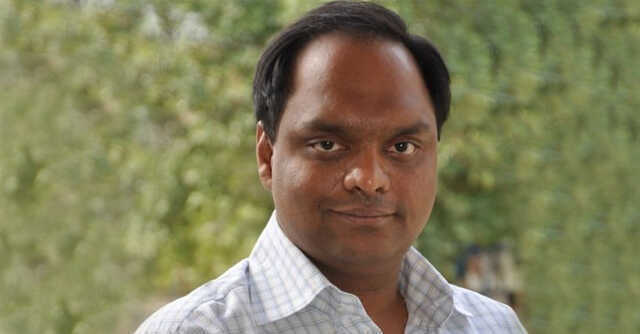

Much like the many other industries, even though the assembly process of battery packs is well established here, India is still an importer of battery cells – the key component for battery packs for electric vehicles (EVs) etc.. All of this may change starting 2022, according to Nitin Gupta, chief executive of Attero Recycling. In an interview, Gupta states that his company is ready to supply critical components required for manufacturing battery cells in India – even though reserves of elements such as cobalt, nickel, graphite and lithium aren’t available in India. Edited excerpts:
Can India make its own batteries, from end to end, at any point?
There are roughly 280 companies that sell battery packs in India, which includes battery management and thermal management layers atop the cells. Some of these companies import fully made batteries from China, while others import cells and pack them in India.

There are about eight large Li-ion cell manufacturers in the world, which include LG Energy Solution, SK Innovations and Samsung SDI in Korea, CATL in China, Panasonic in Japan and a few more. None of them have cell manufacturing facilities in India, as yet.
However, the first steps are falling in place. Amperex Technology Limited (ATL), owned by TDK Corp, Japan is in process of setting up a cell manufacturing plant in the outskirts of the National Capital Region's Gurgaon area by September 2022.
Can this be done without depending on imports from other nations?

So far, there is no cell manufacturing in India. Cobalt, nickel, lithium and graphite are required in cell manufacturing, and not pack assembling. Today, none of our recycled output goes to cell makers in India, because there are none. Once they are functional, we believe that we can source critical cell components for them without needing imports.
We believe that what we are producing has great scope, because right now, the Indian government is largely pushing its electric vehicle (EV) policy. Alongside environmental concerns, they are also doing so to reduce the forex bill of oil imports. However, in terms of batteries, India does not have reserves of cobalt and lithium. As a result, by pushing for EVs, we will effectively replace our dependence on Saudi Arabia and China — which controls 98 percent of the world’s lithium supply.
To address this, the government has created a public sector undertaking (PSU) organisation to acquire cobalt and lithium mines outside the country. We believe that if a recycling policy is adopted, the country’s cobalt, nickel and lithium needs can be addressed through recycling our own e-waste itself.

Where does India stand right now – in terms of policies to effectively recycle e-waste back into manufacturing?
The Ministry of Electronics and Information Technology (MeitY) has a draft policy paper, called ‘Circular Economy in the Electronics and Electrical Sectors’, which was introduced in May 2021. The paper talks about companies in India ensuring a minimum input of recycled materials in their output. But I believe this will likely take at least six more months to be implemented. This can help establish a circular economy in India.
Such a policy offers big promises. For instance, right now, India is a net importer of tin ingots. The latter is now used in lead-free solder, which is made of tin and silver. By recycling e-waste in solders, by the end of 2022, Attero can ensure that India becomes a net exporter of tin ingots – instead of importing so far. In fact, we are already on the way to matching this claim.

Other policies are also being adopted by the government in order to incentivise various industries to come to India. For instance, the government has a production-linked incentive (PLI) scheme that seeks to attract cell manufacturers around the world to come and make the cells in India. This can help us further strengthen our local electronics ecosystem, and go beyond just assembling facilities in the country.
Which companies are so far working with you for recycling initiatives?
In terms of Lithium-ion recycling, today we work with all major OEMs, such as Samsung, LG, Flextronics, Oppo, Vivo, Acer and so on. In the telecom sector, all batteries disposed off by Reliance Jio come back to us for recycling. In automobiles, batteries from Tata Motors, Toyota, Hyundai and Maruti Suzuki come back for recycling.

We’ve also explored exporting our recycled output to Tesla, who are happy to purchase it from us. However, due to the covid-19 pandemic, the deal could not be finished yet. There’s no agreement signed as yet, but we’ve held initial conversations with Tesla.
Also read: Exclusive: Attero Recycling courts Tesla to supply battery materials for its Gigafactory
Do you also directly work with consumers to retrieve end of life cycle products?

We are collecting end of life devices from 1,400 cities across India – from small businesses, service centres and large manufacturing facilities too. We have started a pilot programme for consumer-level collection of devices, but not on a full-fledged scale. We plan to roll this out extensively within the next month.
We have also launched a franchisee programme to set up recycling plants across India. Currently, some of these outlets are becoming operational in various states. By end-2022, we hope to have significant coverage from these plants in terms of recycling volume as well as geographical areas covered.