
Exclusive: Attero Recycling courts Tesla to supply battery materials for its Gigafactory
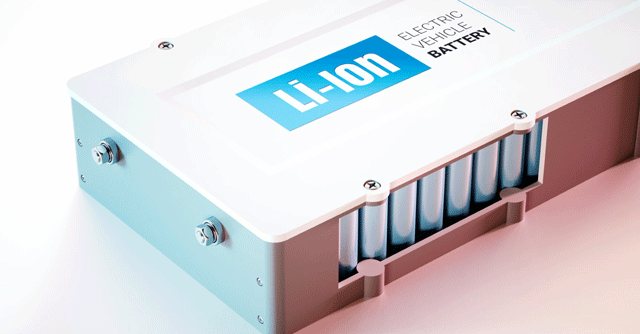

Indian e-waste recycling company, Attero Recycling, has reached out to electric vehicle maker Tesla to supply battery materials for its Gigafactory, according to a senior executive from the company.
“We’ve explored the possibility of exporting our recycled (battery material) output to Tesla, who are happy to purchase it from us. However, due to the Covid-19 pandemic, the deal could not be finalised. There’s no agreement signed as of now, but we’ve already held initial conversations with Tesla for such an arrangement,” Nitin Gupta, co-founder and CEO of Attero Recycling, said in an interaction.
Once complete, Tesla expects its Gigafactory to be the biggest building in the world, and entirely powered by renewable energy sources. According to the Tesla website, "materials in a Tesla lithium-ion battery are recoverable and recyclable". The site explains that battery materials "are refined and put into a cell, and will still remain in the cell at the end of their life, when they can be recycled to recover its valuable materials for reuse over and over again...None of our scrapped lithium-ion batteries go to landfilling, and 100% are recycled."

Gupta, on his part, said that the early-stage talks with Tesla do not hint at the possibility of the company setting up a battery assembling or cell manufacturing plant in India. “In my opinion, at the start, Tesla may only look to import its fully-made cars to India. Their phase two could be to start assembling their cars in India, and a third and final step of their India journey could be to setup a Gigafactory in India. The latter, I believe, is still quite far away,” Gupta said.
A Tesla spokesperson could not be reached for comment at the time of publishing the story.
Even as Tesla has expressed its intent to begin manufacturing its own batteries, it currently sources its batteries from major producers such as Panasonic, China’s CATL, and South Korea’s LG Chem, like all other car makers do.

Tesla has so far created a wholly-owned subsidiary in India, called Tesla India Motors and Energy Private Limited. Earlier this year, the company received approval from the Ministry of Road Transport and Highways (MoRTH) to introduce four of its vehicles on Indian roads. While Tesla has received approval for its cars in India, the company has reportedly held talks with the Indian government to ease import duties of CBUs (completely built units), which currently stands between 60- and 100 percent, but no outcome has been revealed as yet.
In the context of battery manufacturing in India, Attero's Gupta states that while cell manufacturers have not stepped into India en masse, the Indian government’s PLI (production-linked incentive) scheme for Advanced Chemistry Cell (ACC) manufacturing may bring in the bigwigs. “I expect global cell manufacturers to consider India as a market, which would allow us to close the circular economy loop of supplying key components back to the industry we recycled them from, in India,” Gupta said.
India is set to get its first cell manufacturer in the country. In 2020, Amperex Technology Limited (ATL), a subsidiary of Japan’s TDK Corp, acquired 180 acres of land in the outskirts of Gurgaon, India to set up a cell manufacturing facility. The latter is expected to start functioning by the end of 2022.

Gupta added that he expects the draft policy paper by the Ministry of Electronics and Information Technology (MeitY), labelled ‘Circular Economy in Electronics and Electrical Sector’, to be formally adopted in the next six months. The paper states that even though India is the third highest e-waste generator in the world behind China and USA, it only collects about 10 per cent of its waste.
The roadmap starts with a short-term goal of acquiring critical and secondary raw material from e-waste generated in the country. Further steps include extending PLI schemes to manufacturers for using recycled material, enforcing recyclability standards, establishing a sustainable product policy, analysing costs of compliance among manufacturers, spreading awareness among consumers, and so on.
While Gupta says that the adoption of a true circular economy in India is still months away, Ravi Neeladri, CEO of Bengaluru-based Cerebra Green, says that the initial steps are already in process. “The government is enforcing compliances for OEMS in India already. Desktop manufacturers such as Acer, Dell or Lenovo are being asked to recover 50 percent of devices that each of them manufactured six years ago,” he says.

Neeladri also adds that recycling life spans are being decided based on product categories. “For laptops, the life span is earmarked at five years, while appliances such as air conditioners have 11 years. Brands do not have to necessarily collect their own old devices, but recover by volume of devices they made – and refurbish them in their assembly process,” he said.