
Technology is guaranteeing more good days for Britannia’s biscuits biz
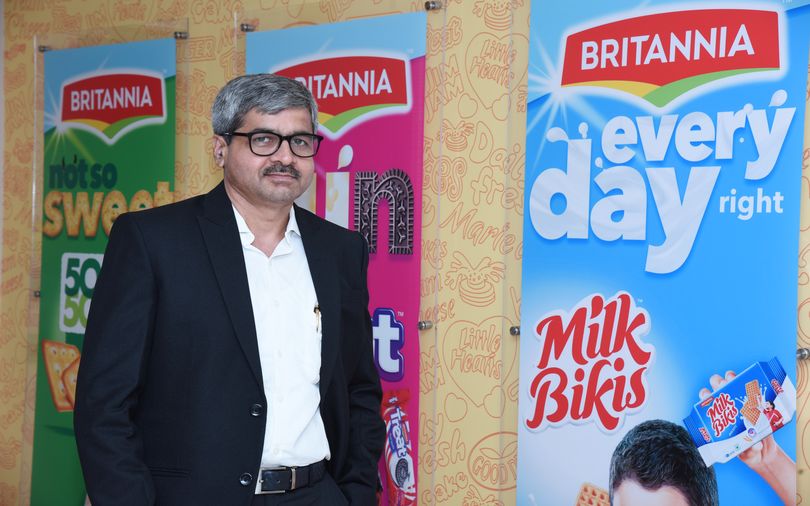

Every now and then, the machines at Britannia’s biscuit factories miss a beat. As a result, its Good Day, 50-50 or Tiger biscuit packets end up being a couple of grams heavier or lighter. Either way, the company stands to lose money. Until a couple of years ago, this irregularity was only spotted more than an hour later when factory employees weighed sample packets from each batch. For a company that dominates the country’s biscuit industry with more than 30% market share, such delays can be ill-afforded.
Now, with Internet of Things (IoT) being increasingly deployed at 126-year-old Britannia’s factories, the machines flag and alert the plant operator as soon as any packet from the assembly line fails to meet the specified weight.
"The operations manager can then intervene and rectify this immediately and hence prevent any further loss," Harish Navarathna, head of IT at Britannia, told TechCircle. “While we do have enough technology to make the machines talk to each other and rectify this automatically, it does not make economic sense as yet.”

He said that such technology-based initiatives have helped Britannia boost its profitability, productivity and efficiency at all levels, though he couldn’t put an actual number to it.
Implementing these technologies at all its plants could bring about greater savings. The executive said this is one reason why Britannia is trying to bring production in-house, as it is difficult to convince manufacturing partners to make such investments.
"When you want to get into premium biscuits, you need better technologies at the plants, which at the corporate level we can afford. It has an impact on the quality and freshness of the product," Navarathna said.

While IoT has helped prevent wastage, analytics has helped improve Britannia's production planning. It has developed an algorithm to identify demand clusters, which often cut across state borders.
While the company was previously making such estimations manually, the data analytics algorithms have automated the procedure. It was a process that began in 2013 using SAP technology.
"We have identified 20-odd demand clusters for the country and run the algorithm based on the data collected to see which production plants are best suited to produce each product to ensure the cheapest delivery," said Navarathna.

Britannia has more than 115 stock keeping units (SKUs) at over 100 production locations and distributed through 50 depots. The company has managed to nearly halve inventory levels at the depots and distributors. Also, with better analysis, it has been able to reduce the non-availability of certain products with distributors by half.
Navarathna also said that while Britannia was looking at several artificial intelligence (AI) and machine learning (ML) models for predicting demand trends across seasons, it has not implemented anything in this regard just yet.
"We are working towards better distribution to the final stores. We have enabled salesmen with outlet-level prediction on what SKUs should be going to certain outlets based on past data, but these are not necessarily AI models yet," he added.

The AI model Britannia is working on needs more data to work better.
"It is similar to the profile identification or product recommendation models that we see on e-commerce platforms," Navarathna said.
He said Britannia would also want to find out if there is a trend of declining demand in a particular locality for a particular SKU, so that they can think about how to win back customers.

The company is also using on-premise server infrastructure while using several software products that are available only on the cloud. Navarathna said that Britannia does not require real-time data as of now.
"We had invested a lot. Cloud is still evolving a lot. Five years from now, when we need to refresh our servers, we could move to the cloud too," he said, adding that some emerging technologies are not yet cost-effective in India.