
Using new tech to speed up production, develop autonomous vehicle: Tata Motors' Petkar
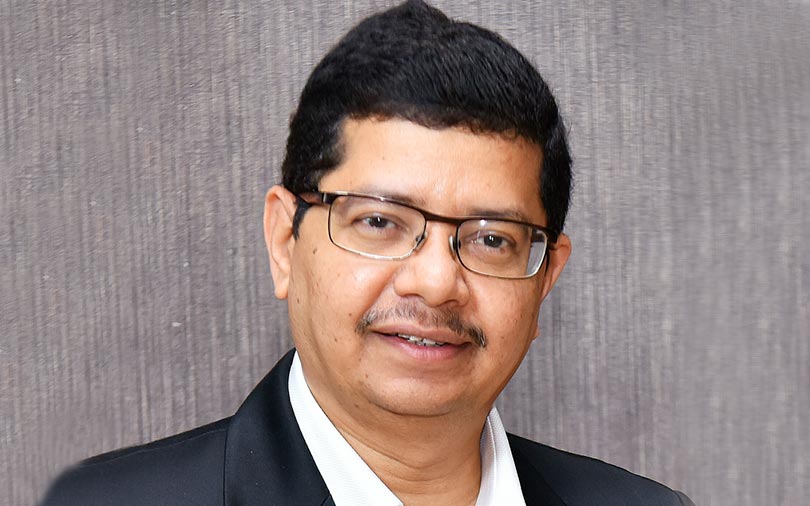

Tata Motors’ factory floors are a ballet of heavy machinery connected and coordinated by information systems that can predict production volumes, sniff out failure risks, and crank up machine efficiency up to 10%. Besides factory-sniffing, error-proofing Industrial Internet of Things, there is nifty software that can simulate a product, helping it condense from vapour to reality much quicker than any other old monolithic setup. Clearly, all these AI and IoT stirrings on the Tata Motors’ factory floor result from a massive spend in research and development -- nearly Rs 2,400 crore, to be sure, for the financial year 2017-18. In order to take a closer look at the car-churning machines of India’s largest automaker by revenue, TechCircle caught up with chief technology officer Rajendra Petkar. Edited excerpts:
How much investment has gone into emerging technologies, both in terms of expenditure and human resources?
On average, Tata Motors has been hiring over 500 cadres every year since 2016, for the following functions: Engineering research centre, manufacturing, engineering, quality, sales and marketing, operations, corporate, etc. Around 8% to 10% of annual research and development spend is being made towards advanced and emerging technologies.

While a major chunk of our hiring happens through universities and institutions, we have been engaging with many job applicants across social platforms.
How is the company using newer technologies such as Industrial Internet of Things (IIoT) to speed up production?
The basic principle of Industry 4.0 is creating an intelligent network by connecting machines, work pieces and systems. In the journey towards Industry 4.0 at Tata Motors, we are using Manufacturing Execution System (MES) as a bridge between the enterprise system and handling the product complexity at the shop floor layer to link the market demand to production schedules at different levels such as assembly, aggregation and components. MES primarily helps us in proper production scheduling, product quality improvement by error-proofing and allows access to real-time reports.

For speeding up production, Tata Motors is currently investing in the following modules:
1. Machine utilisation module: 10% improvement in machine use by capturing real-time data and analytics on Overall Equipment Effectiveness and engaging the workforce to improve the efficiencies.
2. Engine volume prediction: By capturing data of machine components, finished engine inventory, and engine demand from general assembly in terms of product mix (petrol, diesel, turbo charged, etc.); performing analytics to indicate setup change/batch size, engine assembly sequence, shift planning, etc., to ensure seamless engine supply to general assembly.

3. Maintenance module for uptime improvement: Enhancing machine features to capture early real-time signals of potential failures and relevant peripheral data to do analytics for prediction of potential failure mode.
4. Smart energy management: Real-time mapping of energy consumption, along with manufacturing data, for optimising energy consumption with support of analytical tools.
5. Predictive quality management: Using advanced analytics to perform real-time quality-related data mining and analytics to continuously monitor and improve quality at each opportunity.

Has there been a significant change in the entire process operation of the company where supply, production and sales are streamlined?
At Tata Motors, the entire value chain is integrated through various information technology (IT) platforms. The integration of all the processes across value chain through IT enablement fosters transparent communication, faster information-sharing and speedy decision-making. MES has helped significantly in improving the production system.
Key benefits of MES are:

· Scheduling, sequencing and broadcasting of daily production line-up to all aggregate shops for ensuring the correct availability in the assembly line in line with the required sequence.
· Improving the product quality through error-proofing (check before fitment) and poka yoke (mistake proofing) of the critical process and the parts.
· Handling the product complexity by the kitting process (collection of parts with respect to models) and Pick to Light system (selection of the correct part)

· Big data analysis of production management, quality management and line loss for productivity and line efficiency improvement. Using the Andon System, line operators record real-time losses of the assembly line into MES.
Additionally, use of digital factory simulation software for new line installation helps in building the process model for commissioning throughout the analysis of the system and process, before its implementation.
Product simulation using
product lifecycle management and digital factory is helping in quicker product launch and its production.
What about connected cars or Internet of Things (IoT) in vehicles?
Tata Motors is working on connected car technologies to offer advanced connectivity features as part of its autonomous vehicle programme. We, at Tata Motors, understand the need for a connected ecosystem that can integrate into the digital lives of customers. With the aim to develop and innovate technologically leading products that excite customers, we are working with technology partners, to bring the digital lives of our customers into the cars they drive. Connected vehicle technology uses artificial intelligence, advanced machine learning, and the IoT to enhance driving experiences.
Tata Motors has already provided connected-vehicles technology for its commercial vehicle customers, through its telematics solution platform Fleetman. In passenger vehicles, Tata Motors has demonstrated various concepts at multiple occasions, showcasing its capability.