
Porsche turns to 3D printing to manufacture parts for its classic cars
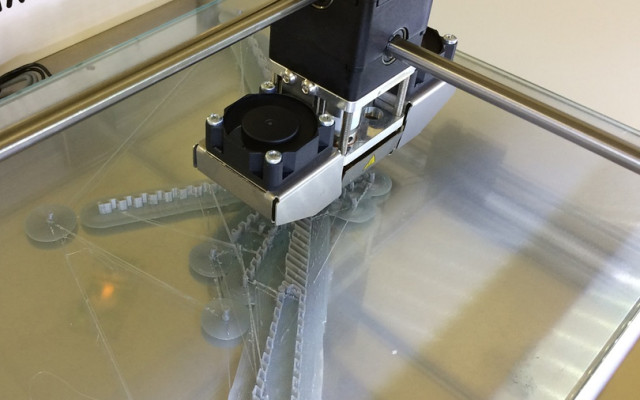

German luxury automaker Porsche has turned to 3D printing to combat a shortage of parts for its classic cars.
The company's Porsche Classic division, which exclusively handles classic cars, is using 3D printers to make steel and plastic parts. It is resorting to an additive manufacturing (AM) process that can churn out parts of the same size and specifications that were originally produced by the company.
Porsche's decision was likely influenced by the fact that 3D printing these parts would be cheaper than starting an entirely new line of production for old parts.

Additive manufacturing refers to a process by which digital 3D design data is used to build a component in layers by depositing material.
The German automaker used a process called selective laser melting as a part of its AM strategy to create the metal parts.
As part of the process, a light beam is used to melt a layer of powdered steel kept on a plate to a desired shape. The process is repeated until the entire part is printed out.

As for the plastic parts, Porsche used another AM technique called selective laser sintering. The technique uses a laser as the power source and aims it automatically at points in a space defined by a 3D model. which then binds the material together to create a solid structure.
However, Porsche used the process differently. To 3D print the parts, it heated the material just below its melting point and later used a laser to fuse it together into shape.
The automaker is said to be 3D printing only nine different parts currently, including the 959's clutch release lever.

Automakers are increasingly using 3D printing to meet their production requirements. Last month, French carmaker Bugatti had 3D-printed a brake caliper.